Engine Science 101: Maximize Power Through Sound Engine Design

Heavy Breather A/C. Courtesy Harley-Davidson, Inc.
Most V-Twin owners begin engine performance upgrades with a free-flowing air cleaner and high-flow exhaust system. Then they add an EFI tuner along with a dyno tune to optimize the combination. But some combinations never perform up to expectations regardless of the amount of time spent tuning or the tuner’s expertise. This is because tuning actually starts with engine design and parts selection. And some engines were never designed properly. As a result, no amount of tuning can make a poorly conceived engine perform up to expectations.
For this reason, it’s important to have at least a rudimentary knowledge of the relationships between various engine design elements, so your engine has the capability of meeting performance expectations before dyno tuning begins. The result will be a more compatible engine combination, providing higher performance and greater sensitivity to each tuning adjustment. And it will be at much less time and cost. Even if you’re not building your own engine, understanding rudimentary engine design will better prepare you to discuss design considerations and parts combinations with your engine builder when starting a performance project.
The best way to end up with a winning engine combination is to start your design efforts with the thought of building a “happy engine.” The term “happy engine” may at first sound strange, but it implies that regardless of what you do during the engine design process, you don’t necessarily need the most radical cam, an outrageous exhaust or the biggest induction system. Instead, choose components that compliment one another, which will provide a collection of compatible parts that work in harmony. Your reward will be a “happy engine” designed and built with synergy that addresses a specific application.
Three major variables influence horsepower: displacement, rpm, and cylinder pressure, which sometimes are referred to as “brake mean effective pressure” or bmep. These three variables evolve into five principle methods for increasing the power of the internal combustion engine:
- Increase Displacement
- Raise rpm
- Improve Volumetric Efficiency
- Maximize Thermal Efficiency
- Minimize Mechanical Friction
The first four methods all have one thing in common—they all raise cylinder pressure. Whenever making a modification or selecting a part, always do it with the thought of raising cylinder pressure on the intake cycle and relieving cylinder pressure on the exhaust cycle.
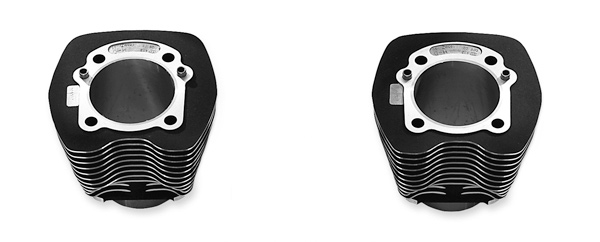
Big-Bore Cylinders increase engine displacement and torque.
Adding displacement is king when it comes to increasing power because it is the easiest method for raising cylinder pressure over the entire rpm range, particularly down low where torque rules. Increasing displacement allows the engine to draw in more air/fuel mixture during each cycle for higher cylinder pressure, resulting in greater torque and horsepower.
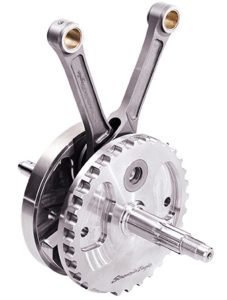
A stroker crankshaft increases engine displacement and torque.
There is a relationship between torque, rpm and horsepower. In simple terms, horsepower is equal to rpm multiplied by torque. And torque is determined by the amount of cylinder filling. The greater the cylinder fill, the greater the cylinder pressure, thus the greater the torque will be. If the level of torque is maintained, increasing rpm automatically increases horsepower. Even if torque drops, as long as rpm increases at a greater rate than the reduction of torque, horsepower increases. Savvy engine builders concentrate on improving torque. They know that if torque is increased, horsepower will take care of itself. They also understand that higher rpm can lead to greater horsepower.
Increasing volumetric efficiency (VE) amounts to filling the cylinder with a greater amount of air/fuel mixture, thus cylinder pressure is increased. VE is primarily controlled by intake and exhaust tract design and camshaft specifications. For optimized performance, always concentrate on increasing volumetric efficiency within the rpm range the engine operates. In the case of a race engine, concentrate on improving VE at the higher rpm levels. For a street engine, low and midrange rpm is usually most important.
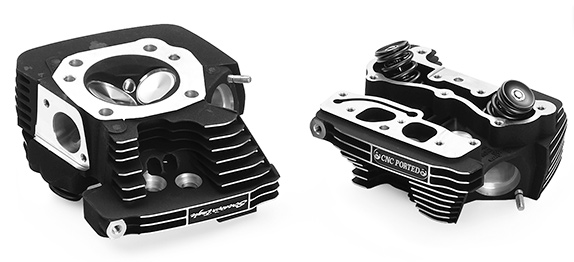
High-flowing cylinder heads can increase volumetric efficiency.
Although filling a cylinder with more air/fuel mixture can result in greater power, the real key to more power is not only how much air/fuel mixture is burned but also how much is converted into heat energy. Thermal efficiency refers to how efficiently the engine uses energy from combustion heat to apply pressure on the piston during the power stroke. As thermal efficiency increases, more combustion heat is used to apply pressure on the piston and less heat is expelled through exhaust gases. Consequently, exhaust gas temperature is reduced. Optimizing combustion chamber design, compression ratio and ignition advance along with the use of thermal coatings and exhaust header heat wrap can maximize thermal efficiency.
Some of the power produced by the engine is used to overcome the resistance to motion of rotating and reciprocating parts. The difference between the power produced in the cylinder and that produced at the crankshaft is considered frictional horsepower loses and often referred to as mechanical efficiency. In part, mechanical efficiency is a function of rpm and piston speed. Generally, the higher the rpm and piston speed, the greater the frictional losses. Frictional power losses take place between every component, including the crankshaft, piston rings, bearings, valvetrain components, and lubrication system. Crankcase flexing also contributes to frictional losses, particularly with very large displacement engines. The Sportster engine is more mechanically efficient than the Big Twin due, in part, to its lighter flywheel mass, rods and piston assemblies. All power lost to friction is converted into heat and dispelled through the V-twin’s oiling and air-cooling systems.
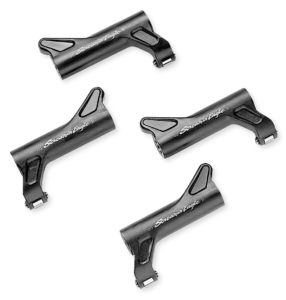
Roller rocker arms reduce friction and can improve reliability.
Assembling an engine without piston rings and valvetrain components, and then rotating the crankshaft by hand can illustrate frictional power losses. If you then install the piston rings and valvetrain parts and again rotate the crank, you will notice more effort is required to turn the fully assembled engine. The additional effort represents the frictional power losses. Of the total engine frictional loses, roughly 75 percent is attributed to the piston and rings, and half of this amount is consumed by the oil ring. Bore diameter and stroke length have a significant influence on frictional losses due to the piston and rings. Minimizing mechanical friction is often the difference between a winning and losing engine.
When designing an engine, consider that all power is made within the combustion chamber—between the top of the piston and roof of the cylinder head. Also, consider that airflow is the name of the game, and it is of paramount importance for making power. Since combustion efficiency and airflow are closely related to the cylinder head, cylinder head design is crucial to producing maximum power. As such, although an engine is built from the bottom up, it is always designed from the top down — starting with the cylinder head. (TVR)